Abstract: Aiming at the problem of tungsten inclusion during the prefabrication of
carbon steel pipes for asphalt tankers and chemical tankers, the argon arc welding process was improved. Firstly, check the relevant information to analyze the cause of the tungsten inclusion; then check each link of the site construction one by one, and find that the welding current value selected by the welder greatly exceeds the allowable value in the welding procedure specification, which directly causes the tip of the tungsten pole to melt. At the same time, the cutting of the tip of the tungsten pole is not standardized. Finally, adjust the welding process according to the actual production situation; choose large-diameter tungsten electrodes, and use high-current welding before conducting welding process approval tests. The results show that the qualified rate of X-ray inspection of pipe joints has reached 100%, and the welding procedure evaluation has been approved by China Classification Society (CCS), completely solving the quality problem of tungsten inclusion.
Introduction
Argon tungsten arc welding is a welding method that uses argon gas protection, tungsten rods as an electrode, and does not melt the tungsten electrode during welding. At present, this welding method is especially suitable for the welding of thin plates and is mostly used for welding non-ferrous metals such as stainless steel, aluminum, copper and their alloys. Argon arc welding is widely used in shipbuilding, especially in the production process of carbon steel pipe systems. To fully ensure the quality of the root of the welding seam, the enterprise usually uses argon arc welding to make the bottom plus flux cored wire gas shielded welding to fill the cover.
During the processing and prefabrication of asphalt tankers and chemical tanker pipes, to improve work efficiency, the production workshop adopts high-current welding in argon-arc welding. There were defects in tungsten inclusions after the X-ray inspection of the welding seams of a large number of carbon steel pipes, which caused a lot of rework after welding, and the production plan was also affected. For this reason, on the basis of analyzing the specific reasons for the tungsten inclusion, starts the process of solving the quality problem in this article.
1.
On-site situation investigation and cause analysis
1.1
Welding current
The causes of tungsten inclusion in argon arc welding are shown in Table 1.
According to production experience, the greatest possibility of on-site problems is the influence of the welding current described in item (1) in Table 1. For this reason, the welding technicians focused on the actual measurement of the welding current on site, and found that in order to improve work efficiency, the welders in the workshop did have the problem of using large parameters for argon arc welding: the welding current specified in the welding procedure specification was 110 to 120 A and is increased to more than 160 A; the maximum is 180 A.
Table 1 Causes and preventive measures of tungsten inclusions
Causes |
Preventive measures |
(1) If the current is too great and the diameter of the tungsten electrode is small, the tungsten electrode will melt. |
(1) Choose the appropriate welding current and tungsten electrode diameter. |
(2) Collision happens between the tungsten electrode and welding wire. |
(2) Avoid collision between the tungsten electrode and welding wire or in the working process. |
(3) Oxidizing gas such as CO2 is not correctly used. |
(3) Use inert gas instead. |
(4) Poor argon gas protection causes tungsten electrodes to burn. |
(4) Make the tungsten electrode well protected. |
1.2 Tungsten electrode
1.2.1 Manufacturers and grades of tungsten electrodes
Electrode diameters and end shapes of Tungsten are important factors affecting the quality of argon arc welding. The shipyard currently uses WC-20 cerium tungsten electrodes with a diameter of 2.4 mm. This kind of electrode has excellent arc starting performance at a low current, and the arc maintenance current is small. It is often used for welding pipes, stainless steel products and small and delicate parts, and no tungsten inclusion has been found so far.
1.2.2 Diameters of tungsten poles
The diameter of the tungsten electrode determines the structural size, quality and cooling method of the welding torch, which affects the labor intensity and welding quality of the welder. Therefore, we focus on the matching relationship between the diameter of the tungsten electrode and the welding current in this article. The diameter of the tungsten electrode is generally selected according to the thickness of the weldment, the amount of the welding current and the polarity of the power supply. Each tungsten electrode has an allowable current. When the allowable current is exceeded, the tungsten electrode will be melted and volatilized due to overheating, resulting in unstable arc and tungsten inclusion defects in the welding seam. The shape and size of the tip of the tungsten electrode recommended for pulsed argon arc welding are shown in Table 2.
Table 2 The shape and size of the tip of tungsten electrode recommended for pulsed argon arc
Diameters of Tungsten
ะค/mm |
Diameters of Tips d/mm |
Angles of tips α/( °) |
Current /A |
The diagram of dimension of tungsten |
Constant Current |
Pulse Current |
1.6 |
0.5 |
25 |
8 to 50 |
8 to 100 |
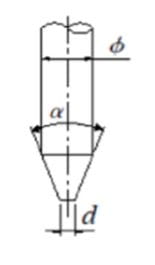 |
1.6 |
0.8 |
30 |
10 to 70 |
10 to 140 |
2.4 |
0.8 |
35 |
12 to 90 |
12 to 180 |
2.4 |
1.1 |
45 |
15 to 150 |
15 to 250 |
3.2 |
1.1 |
60 |
20 to 200 |
20 to 300 |
3.2 |
1.5 |
90 |
25 to 250 |
25 to 350 |
If the diameter of the tungsten electrode is too large, the current density will be small; the temperature of the tip of the tungsten electrode will be insufficient, and the arc will drift irregularly at the tip of the tungsten electrode, that is, the arc is in an unstable state; the argon gas loses its function of protecting the arc, and the molten pool is oxidized. If the diameter of the tungsten pole is too small, the current density will be too high. The temperature at the tip of the tungsten pole will reach or exceed the melting point of the tungsten pole, and the melted tungsten will form a droplet and fall into the molten pool, causing tungsten inclusion; the arc also flutters with the droplet and becomes unstable, which destroys the argon protection zone, oxidizes the molten pool, and deteriorates the formation of welding seams.
1.2.3 Tip shapes of tungsten
The tip angle of the tungsten electrode ground on site is less than 30°, and the tip is extremely tapered; it is very easy to break under the condition of high current. Checking the used tungsten electrodes on site, it is found that some parts are broken and the surface is black. This phenomenon indicates that the tungsten electrode has been broken in the welding process and the fragments have fallen into the welding seam. If the problem is not detected in time, it will cause tungsten inclusion. It is mentioned in relevant documents that the tungsten pole tip can be ground into a platform of about 1mm, which makes the welding current stable and concentrated, and the tungsten pole tip is not easy to melt and burn. At the same time, attention should be paid to the arc ignition method, and the contact short circuit arc ignition method cannot be used. Otherwise, the loss of the tungsten electrode will be great and the end will be easily damaged.