Welded steel pipe, a marvel of engineering and ingenuity, has been an essential component in the development of modern infrastructure. It is a type of pipe made of steel plates or coils that are bent into a circular shape and then welded together. This process creates a strong and durable pipe that can withstand high pressure and extreme temperatures. Welded steel pipe has played a crucial role in shaping our modern world by providing reliable infrastructure solutions across various industries. Its strength, durability, versatility, and cost-effectiveness make it an indispensable component in countless projects worldwide. As technology advances further and new materials emerge on the market, the
welded steel pipe continues to stand as a testament to human innovation and progress in engineering. One of the key advantages of welded steel pipe is its versatility. It can be used in various industries such as oil and gas, construction, water supply, and transportation. Its strength allows it to carry heavy loads over long distances, making it ideal for underground pipelines or overhead bridges. Additionally, its corrosion resistance ensures longevity even in harsh environments. Furthermore, welded steel pipe offers cost-effective solutions for many applications. The manufacturing process is efficient and relatively inexpensive compared to other types of pipes like seamless steel pipes. This makes it an attractive option for large-scale projects where budget constraints are a concern. However, like any other material, there are also limitations to consider when using welded steel pipe. For instance, its size is limited due to the welding process itself. Additionally, welding may weaken the material at the joints if not done properly.
With the rapid development of China's industry, the requirements for quality of steel products are becoming more and more stringent. Among them, general structural pipes, such as general buildings, civil engineering, iron towers and other steel pipes are basic materials in the construction industry. The quality of welded steel pipes is mainly evaluated through testing methods such as flattening tests, mechanical tensile tests and high-temperature fatigue tests. Among them, the flattening test is to test the ultimate plastic deformation ability of the pipe when it is flattened and deformed without cracks under given conditions. Its advantage is that the test results can be obtained quickly.
The flattening test is one of the methods to check the quality of steel pipes. By analyzing the causes of cracking in the flattening test and taking corresponding measures, cracking in the flattening test of welded steel pipes can be solved. The experiment uses scanning electron microscope (SEM), energy dispersive spectrometer (EDS) and metallographic microscope (OM) and other equipment to analyze the causes of cracking in the flattening test of welded steel pipes in two aspects: metallographic analysis and fracture analysis.
1.
Experimental materials and methods
This tested product is a steel pipe made in China. The steel used is hot-rolled Q235B ordinary carbon structural steel. It has an outer diameter of 26.8mm and wall thickness of 2.75mm. Q235B uses an 80t oxygen top-blown converter (BOF) for smelting. The plant does not use a ladle refining furnace (LF) for refining. The cross-sectional size of the continuous casting billet is 180mm × 1500mm. Its chemical composition is shown in Table 1, and the steel plate production process and performance parameters are shown in Table 2. The production processes of welded steel pipes are: steelmaking → continuous casting → hot rolling → pickling → slitting → curling → pressure measuring devices → welding → internal and external deburring → cooling → neck setting → cutting. The chemical composition of the steel pipe complies with the standard requirements of GB/T699-2008 "High-quality Carbon Steel".
Table 1
Chemical composition of the sample
Cut and sample the cracked part of the steel pipe, and cut the cross-section and longitudinal section, as shown in Figure 1. Use tools to open the cracks to prepare fractured specimens. The prepared samples were ground, polished, ultrasonic cleaned, dried, and comprehensively analyzed using scanning electron microscopes, energy spectrometers, metallographic microscopes, and other instruments. The samples were corroded with 4% nitric acid alcohol and then analyzed using a metallographic microscope. Observe its organization.
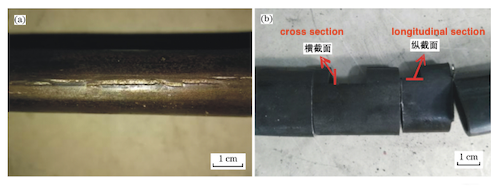
(a) Macroscopic morphology of the sample (b) Sampling positions
Figure 1 Macroscopic morphology and sampling positions of the sample